Solving Errors Faster
Convincing customers with efficient error management
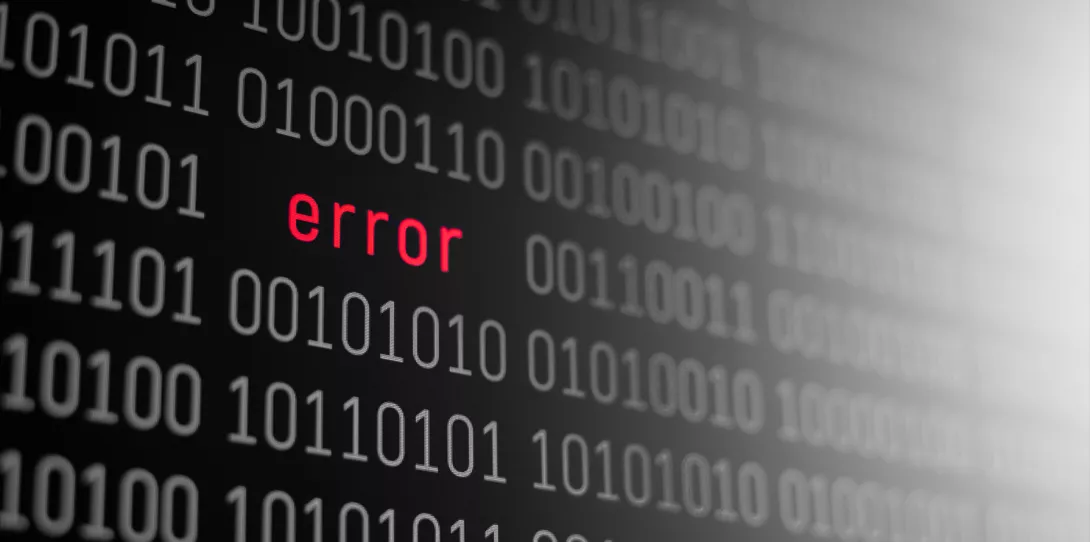
09.04.2025 | Article
Zero errors – this is a widely accepted conception in business. Striving for perfection is a maxim in many commercial areas, especially in quality management. The reality, however, is different. Whether it's material defects in a bicycle, connectivity problems with vehicle software or even issues booking travel: Errors that impact customers can occur in many industries and companies. Unfortunately, it is impossible to avoid them completely. The crucial question for businesses is: Is it possible to rectify errors effectively and, above all, quickly, to satisfy customers and even impress them by handling them correctly?
‘Quality is when the customer comes back – not the product’. This saying, attributed to the founder of a traditional German department store chain, sums up what really matters: It is not only the flawless product that counts, but above all how errors are handled. At the point when something is not working optimally and customers are actually affected, it becomes patently clear how seriously quality is actually taken. Those who act quickly, transparently and in a solution-oriented manner will generate trust and confidence. An error communicated and corrected rapidly and transparently will quickly be forgotten. If customers feel that their concerns are taken seriously, that they can rely on promises and that the problem will be rapidly resolved, then they will come back.
Speed matters when dealing with errors
The right way to rectify errors is not just to fix problems. Building resilience, promoting operational excellence and ensuring customer satisfaction are all essential factors. A key component in customer perception that companies can harness to massively increase customer satisfaction is error correction time. This can be minimized using an optimized process. Benchmarks show that industry leaders are able to completely correct errors within 24 to 48 hours. However, many companies are significantly slower. By taking targeted measures, they can significantly reduce their error correction times. Porsche Consulting has identified six core elements for an optimal error correction process across different industries:
- Holistic process – A structured, end-to-end approach, from identification to remediation, is essential
- Data-driven foresight – Systematic early error detection and centralized data tracking are the basis for effective action
- Cross-functional analysis – Root-cause analysis and problem solving require specialized, interdisciplinary collaboration between different teams and departments
- Continuous monitoring – A robust monitoring system ensures accountability and full remediation and defines clear objectives such as response times
- Responsibilities and communication – Clear responsibilities and decision-making procedures with well-established escalation paths ensure fast and effective action
- Verification and improvement – Effective troubleshooting is ensured by regularly reviewing and confirming the sustainable elimination of errors, followed by the integration of new findings to prevent future errors
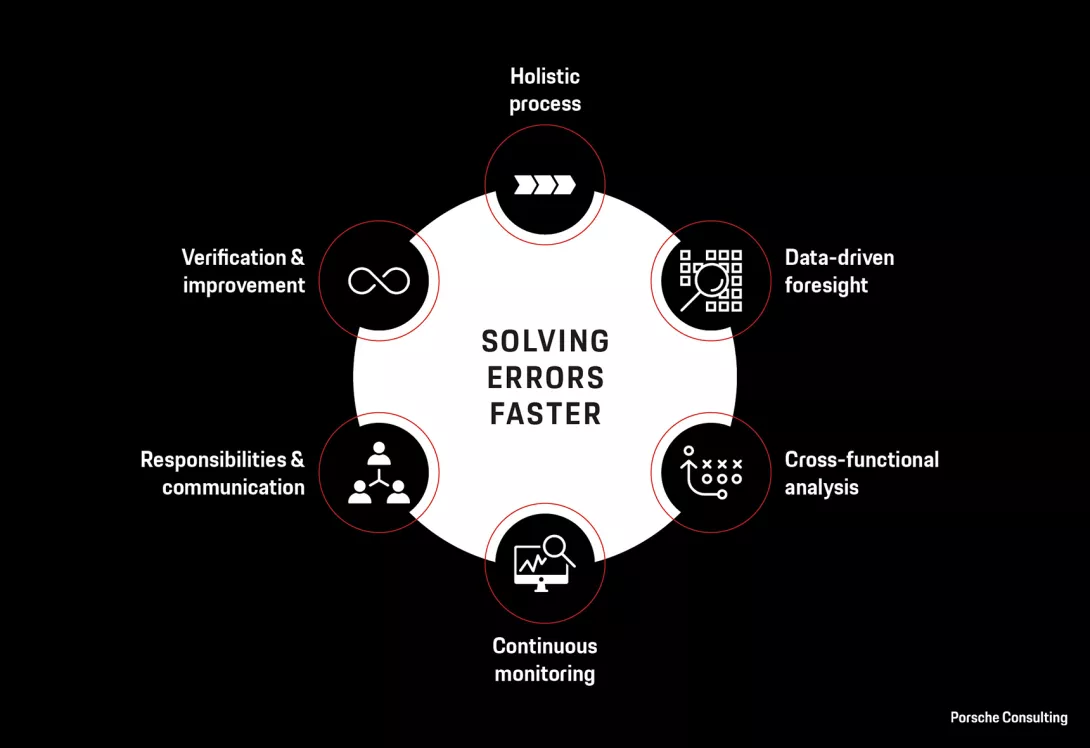
A concrete example from the industry shows how the six core elements work in practice. An international plant manufacturer needed to increase efficiency and reduce costs. In collaboration with Porsche Consulting, the six principles for eliminating errors were introduced. Errors are recorded by a central system. Error data is evaluated at the interface between the engineering and quality departments as well as the suppliers. Cross-functional fault correction teams are deployed centrally in coordination with the plants and the relevant markets.
Solution finding 30 percent faster
A core element of this process is identifying potential errors and problems in the markets as early as possible. Methods such as Causal AI are used primarily in this area by a data analytics team to swiftly identify problems in the field. A central system for all quality indicators was introduced for continuous monitoring. To ensure ongoing improvement, errors are prioritized and tracked according to product safety, frequency and impact on customer satisfaction. By consistently implementing all six principles, it has been possible to reduce the time required for troubleshooting – from detecting an error to implementing a marketable solution – by around 30 percent.
Processing errors offers vast potential
Effective error correction comprises much more than just fixing problems quickly – it is a critical factor for operational excellence, customer satisfaction and long-term business success. The six core elements of an efficient error correction process may seem simple at first glance, but their successful implementation calls for a high degree of organizational networking, procedural discipline and cultural change. Companies that not only manage to rectify errors quickly, but also systematically learn from them, strengthen their competitiveness and resilience in the long term. The potential is enormous: An optimized error correction process can achieve efficiency gains in the double-digit range as well as boost customer confidence over the long term. Companies that are able to manage errors efficiently and in a structured manner will stand out from the competition.
Contact
Consulting that works
You want to get in touch with our experts? Reach out to us.
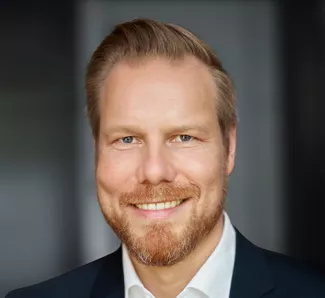